RELIABILITY AND CUSTOMER SERVICE

FORT PIERCE FACILITY

MANATEE FACILITY
OUR SALT-TO-BLEACH PLANTS
Salt-to-Bleach plants are “cleaner & greener” and use the most environmentally friendly bleach manufacturing process in the industry. It is also designated as “Inherently Safer Technology” by the Department of Homeland Security. In October 2010, we opened our first “salt-to-bleach” manufacturing plant in Fort Pierce, FL. In December 2020, we opened our second and newest “salt-to-bleach” manufacturing facility in Manatee County, Florida. Our two salt-to-bleach plants are, by far, the largest and most technologically advanced “salt-to-bleach” manufacturing facilities in the United States.
Unlike our competitors’ plants, our facilities were specifically designed and built to allow expansion, additional capacity, and growth. As our customer base grows, we can continue to meet their needs. Our other manufacturing plants and supply centers ensure we meet each customer’s water treatment chemical needs from Baton Rouge, LA to the Florida Keys.
OUR SUPERIOR DISTRIBUTION SYSTEM
With our manufacturing facilities in Miami, Manatee County, FL, Fort Pierce, FL, Brunswick, GA, Ellisville, MS, and our distribution terminals in Jacksonville, FL, and Dothan, AL, we are uniquely positioned to provide superior service and unequaled redundancy to our customers. All of our locations are in close proximity to major highways and rail lines. Combined with our emergency response system, and support from the state’s emergency management network, provide vital backup in the event of a disruption of supply in any one location.
Our distribution system in the Southeastern U.S. includes a dedicated fleet of Bleach Railcars, over 100 tractor-trailers, and 100 tankers to ensure timely delivery during peak demand periods.
We are the only Florida bleach manufacturer to also have a dedicated fleet of bleach railcars, which enables us to transport large quantities of bleach across the state quickly, efficiently, and economically. Our entire fleet of tankers and railcars is 100 percent “dedicated” – it delivers only bleach and, only for Allied customers. Plus, all of our bleach tankers are fiberglass, to ensure product quality and freshness and eliminate any possibility of cross contamination. Our trucking fleet includes 40 flatbed trailers, 10 dedicated sodium hydroxide tankers, and 6 cherry pickers to service our customers’ dry goods needs, chlorine, and sodium hydroxide. We typically make over 100,000 bleach deliveries each year throughout the Southeastern United States, demonstrating the size, strength, and capabilities of our distribution system. We also have an international division servicing Latin America and the Caribbean.
Our multi-branch network provides guaranteed backup supply and reduces carbon footprints while also ensuring timely distribution and reliable deliveries to our customers, year-round, in virtually any emergency and regardless of adverse weather events. This is a key consideration in our hurricane-prone area (southeast). Our multiple manufacturing and distribution facilities enable us to provide our customers with backup and redundancy that “single facility” competitors simply cannot match.
The redundancy of our multiple plant locations, all which are in close proximity to major highways and rail lines, together with our emergency response system, and support from the states’ emergency management networks, provide vital backup in the event of a disruption of supply in any location due to hurricanes, tropical storms or other events.



OUR TECHNOLOGY: HOW IT WORKS
We are committed to providing a secure, dependable supply of the highest-quality sodium hypochlorite (bleach), produced in an environmentally friendly manner. Toward that end, our two salt-to-bleach plants incorporate redundant systems not found in any other salt-to-bleach plants. Many other plants must shut down for days in order to perform required maintenance, whereas, our two plants are designed to operate and maintain bleach production even during required maintenance activities, assuring customers of uninterrupted supply.
The salt-to-bleach manufacturing process consists of four basic steps:
• First, high-purity salt (NaCI, or sodium chloride) is dissolved into water to produce a brine solution
• The brine solution is then purified by membrane and carbon filtration and ion exchange
• The purified brine is then passed through membrane cells and electrolyzed, to produce the two basic ingredients of bleach: sodium hydroxide (caustic) and chlorine gas
• The chlorine gas and caustic solution are continuously combined in a reactor to produce high-quality sodium hypochlorite (bleach), which is chilled during and after the reaction process to preserve freshness. The bleach is then piped to fiberglass storage tanks and loaded for shipment

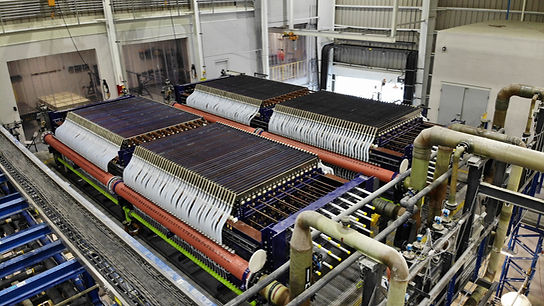


OUR PLANT NETWORK AND PRODUCTS PRODUCED
FORT PIERCE, FL: Our first salt to bleach plant, commenced production in late 2010. It has an on-site rail facility and is located in close proximately to both interstate 95 and Florida’s Turnpike. As such, it is capable of providing bleach for delivery throughout Florida.
MIAMI, FL: Our Miami bleach manufacturing facility is located in Medley. It also has an onsite rail facility, as well as ready access to nearly all major transportation arteries. As such, it is very capable of providing bleach for delivery practically statewide, but typically serves South and Southwestern Florida from Key West to West Palm Beach. Our Miami facility also is equipped to receive and “trans-load” from rail cars to trucks. Our Miami plant also supplies chlorine, hydrochloric acid, sulfuric acid, pool acid, sodium hydroxide, and water treatment products.
DOTHAN, AL: Our Dothan Sodium Hypochlorite terminal provides us the ability to service our customers between our manufacturing facilities and cut down on transportation costs to our customers.
JACKSONVILLE, FL: Our Jacksonville, transloading bleach terminal opened in summer 2012. Providing intermodal rail-tohighway service to facilitate deliveries from our Fort Pierce plant, dramatically reducing the shipping time from the manufacturing facility to our customers throughout North and Central Florida and South Georgia.
BRUNSWICK, GA: Our Brunswick plant manufactures several different strengths of sodium hypochlorite and manufactures sodium bisulfite, which is distributed throughout Florida and its adjoining states. It also has an onsite rail facility and is located near Interstate 95. It serves customers throughout Alabama, Florida, Georgia, and South Carolina.
In addition to high-quality bleach, the plant also supplies chlorine, hydrochloric acid, sulfuric acid, pool acid, sodium hydroxide, sulfur dioxide, sodium bisulfite, and water treatment products.
ELLISVILLE, MS: Our Ellisville Sodium Hypochlorite plant in southeastern Mississippi, is positioned to serve the Florida Panhandle, Alabama, as well as Arkansas and Louisiana. In addition to Sodium Hypochlorite, it also supplies Chlorine and Sulfur Dioxide.
MANATEE COUNTY, FL: Our second and newest, state-of-the-art, salt-to-bleach manufacturing facility commenced production in 2021. This new facility will guarantee all our customers’ needs year-round and in virtually any emergency. The Manatee plant was specifically designed and built to allow expansion, additional capacity, and growth so that as our customers grow, we can continue to meet all their required needs for sodium hypochlorite. The facility is constructed for delivery and pickup by others that are able to pick up products.



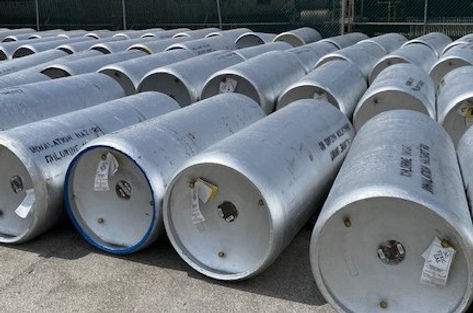

QUALITY MANAGEMENT AND SAFETY

At Allied Universal Corporation, our commitment to quality is evident in every phase of our business. We select our vendors with discretion and perform quality inspections on incoming raw materials for their purity and grade. Our production and packaging procedures have been fine-tuned for high efficiency and quality. We continue to strive for excellence and have implemented Responsible Distribution™ by adopting programs that incorporate product stewardship, hazardous communications, environmental protection, safety training, and security.
At Allied, we believe this is the perfect foundation for total quality in our business. Our Good Manufacturing Practices (GMP), Statistical Process Control (SPC), and Just-In-Time Inventory (JIT) simply complete the profile of a company that belongs on your select list of Certified Suppliers. As part of our efforts to ensure the satisfaction and safety of our customers and in turn the end-user of the product, we place great emphasis on our product quality. We have a dedicated quality control department that utilizes a comprehensive range of analytical techniques to ensure the highest product quality
As part of our commitment to achieving the highest standards of product quality, we focus on the following areas:
• High-quality raw materials and strict product standards
• Dedicated quality control department and personnel
• Multiple layers of filtration utilizing the latest technologies
• Elimination of contaminants and impurities which can contribute to product degradation
• Best manufacturing processes
• Investment in “state of the art” process equipment and technology
• Independent lab testing and analysis Safety First We place a premium on the safety of our employees, our customers, and the end-users of our bleach and other products. Our safety program centers on five elements:
• colored-coded, easy-to-read labels
• material safety data sheets
• a spill prevention control program
• personal protection equipment (PPE)
• safety training seminars
• training of employees
Safety First
We place a premium on the safety of our employees, our customers and the end-users of our bleach and other products. Our safety program centers on five elements:
• colored-coded, easy-to-read labels
• material safety data sheets
• a spill prevention control program
• personal protection equipment (PPE)
• safety training seminars • training of employees
This five-part Responsible Distribution™ Safety Program provides an integrated system to help enhance employee safety and comply with regulatory requirements efficiently and cost-effectively. This emphasis on safety extends to our tankers specifically dedicated to the products they carry so there is no cross-contamination. Allied has tankers dedicated to sodium bisulfite, sodium hydroxide, and more than 100 fiberglass tankers dedicated to sodium hypochlorine. Besides the dedicated tankers, Allied has flatbed trailers with cherry picker type of crane system for delivery of ton containers, as well as a fleet of more than 40 flatbed trailers to service customers’ dry-goods needs. As a pioneer in innovative packaging designed specifically for the safe shipping, handling, and storage of chemicals, Allied has developed options that reduce potential hazards in handling and storage, whether for consumer, retail, wholesale or industrial use. Our packaging includes gallons, recyclable polyethylene econo-drums, 15-gallon and 55-gallon drums, and bulk, ranging in size from one-gallon to 5,000-gallon tanker trucks to 20,000-gallon railcars.
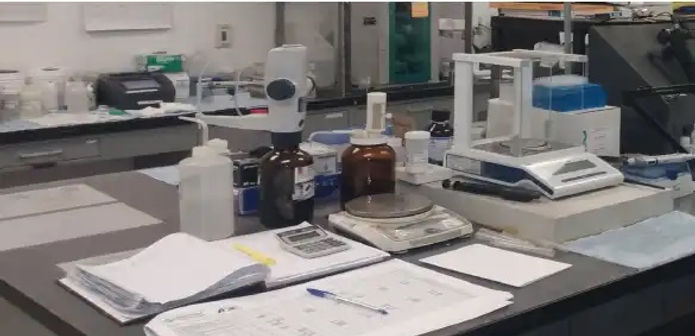
Distribution
With our manufacturing facilities in Miami, Manatee County, FL, Fort Pierce, FL, Brunswick, GA, Ellisville, MS, and our distribution terminals in Jacksonville, FL, and Dothan, AL, we are uniquely positioned to provide superior service and unequaled redundancy to our customers. All of our locations are in close proximity to major highways and rail lines. Combined with our emergency response system, and support from the state’s emergency management network, provide vital backup in the event of a disruption of supply in any one location.
Our distribution system in the Southeastern U.S. includes a dedicated fleet of Bleach Railcars, over 100 tractor-trailers and 100 tankers to ensure timely delivery during peak demand periods.
We are the only Florida bleach manufacturer to also have a dedicated fleet of bleach railcars, which enables us to transport large quantities of bleach across the state quickly, efficiently, and economically. Our entire fleet of tankers and railcars is 100 percent “dedicated” – it delivers only bleach and, only for Allied customers. Plus, all of our bleach tankers are fiberglass, to ensure product quality and freshness and eliminate any possibility of cross-contamination. Our trucking fleet includes 40 flatbed trailers, 10 dedicated sodium hydroxide tankers, and 6 cherry pickers to service our customers’ dry goods needs, chlorine, and sodium hydroxide. We typically make over 100,000 bleach deliveries each year throughout the Southeastern United States, demonstrating the size, strength, and capabilities of our distribution system. We also have an international division servicing Latin America and the Caribbean.
Our multi-branch network provides guaranteed backup supply and reduces carbon footprints while also ensuring timely distribution and reliable deliveries to our customers, year-round, in virtually any emergency and regardless of adverse weather events. This is a key consideration in our hurricane-prone area (southeast). Our multiple manufacturing and distribution facilities enable us to provide our customers with backup and redundancy that “single facility” competitors simply cannot match.
The redundancy of our multiple plant locations, all of which are in close proximity to major highways and rail lines, together with our emergency response system, and support from the state’s emergency management networks, provide vital backup in the event of a disruption of supply in any location due to hurricanes, tropical storms or other events.
• We operate one of the largest independent, private tanker truck fleets in the Southeast Region.
• We are the only dedicated bleach manufacturer with multiple locations, to provide the highest level of redundancy and reliable year-round supply and delivery service, especially during hurricane season
• We are the only Florida bleach manufacturer with a dedicated fleet of bleach railcars
• Our vertically integrated system enables us to provide “single source” full accountability and control
Allied conducts its chemical and transportation operations in accordance with applicable standards and regulations and also cooperates closely with the industry’s national and regional associations.
Allied is a long-standing member of the ACD, and we are fully committed to its guiding principles. We are proud to be a third-party verified member since 1998, and we continue to maintain our commitment to continuous improvement in health, safety, security, and environmental performance of our operations.
Allied Universal Believes in a Firm Commitment to Responsible Distribution
Responsible Distribution is a mandatory third-party verified environmental, health, safety & security program that lets members demonstrate their commitment to continuous performance improvement in every phase of chemical manufacturing, storage, handling, transportation, and disposal. Alliance for Chemical Distribution (ACD) members play a leadership role in their communities as information resources and are eager to provide the same assistance and guidance to local, state, and federal legislators on technical issues relating to the safe handling, storage, transportation, use, and disposal of chemical products.
™
™
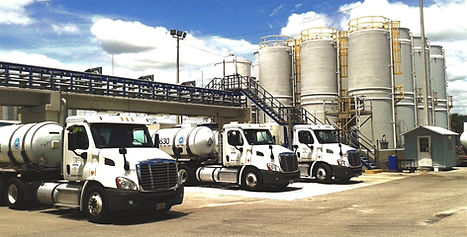


Community

Allied Universal Corporation is proud to be affiliated with these professional and community organizations:
Brevard County Alzheimer’s Association
Baptist Hospital Zoo Kids Dash Run
Baptist Hospital Breast Cancer Fundraiser
American Stroke Association
American Water Works Association
Children’s Resource Center – Miami, Florida
Crohn’s & Colitis Foundation of America
Florida International University Foundation Board
Hibiscus Children’s Center
Susan Komen Breast Cancer Association
West Kendall Baptist Hospital Board
Emergency Information
FOR IMMEDIATE EMERGENCY ASSISTANCE DIAL 911. Spills or releases of certain chemicals may require immediate notification (within 15 minutes of knowledge of occurrence).
Hazardous Response Teams
Highly trained and experienced personnel make up our Hazardous Response Teams. We assist local, regional, and state emergency response teams as needed to stop releases of chlorine, sulfur dioxide, sodium hypochlorite, or any other products produced or packaged for sale by Allied.
Our emergency hotline can be reached 24 hours a day / 7 days a week by calling 786-522-0207. An employee will be notified immediately and your call will be returned promptly. Leave your phone number, with area code, and the reason for your call.
Have the following information ready:
-
Your company name
-
Your name and/or name of additional contact persons
-
Telephone number of the contact person
-
The exact location of the incident, including site entrance requirements
-
Name and quantity of chemical involved
-
Description of incident (i.e. leaking valve)
-
Weather conditions
-
Any injuries and/or evacuations
-
Identify any emergency services already involved (i.e. local public responders)
-
The Allied facility servicing your location
Our hazardous material response teams do not perform any clean-up operations, but Allied works with several environmental mitigation companies who perform these services.
Technical Services
Many members of our management team are part of The Chlorine Institute’s board, issue teams, and task groups, as well as the Alliance for Chemical Distribution. In addition, we serve as chairpersons on several committees.
Typical Requests:
-
Product physical & chemical properties
-
SDS Sheets
-
Chlorine Institute’s technical literature
-
Assistance in solving process issues
-
Materials of construction
-
Assistance with design
-
Safety Training
-
Information for general chemical awareness training
-
Hands-on safety training for 2000# & 150# containers
-
General Technical Help
FOR 24 HOUR CHEMICAL SPILL EMERGENCY ASSISTANCE CONTACT CHEMTREC: 1 (800) 424 9300